Now, I got a couple different sizes, but, one small sheet of 20 gauge. I'm working on cutting all the pieces out for another mini thermojet, and am basically trying to get some experience with stainless before moving up to bigger projects.
Here's the problem. I'm having one heck of a time welding my piece of stainless! I tried it out the first time, and welded two small pieces of stainless pipe together with little problem. A little later I tried to weld one of the intakes for the PJ. Total disaster. the welds were wrinkled and look like crap.
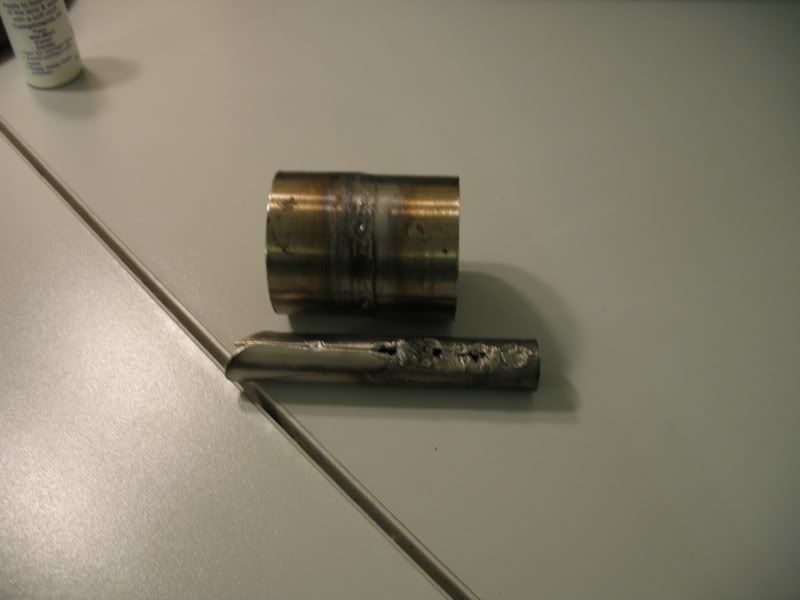
I don't know what my problem is! perhaps stainless just welds ugly... I really don't know. (I'm using a TIG by the way)
my power, no matter how I fiddle with it, too low to melt it, or too high to control it, can't get it to look good! (besides the fact I ruined a good piece of piping...)
power's at 30-50Amps
2% thoriated tungsten electrodes
(no filler metal)
argon at 20cfh flow rate
electrode sharp
well grounded
well cleaned
as far as I know it's 304 stainless (here's the label, I don't know how to read it...)
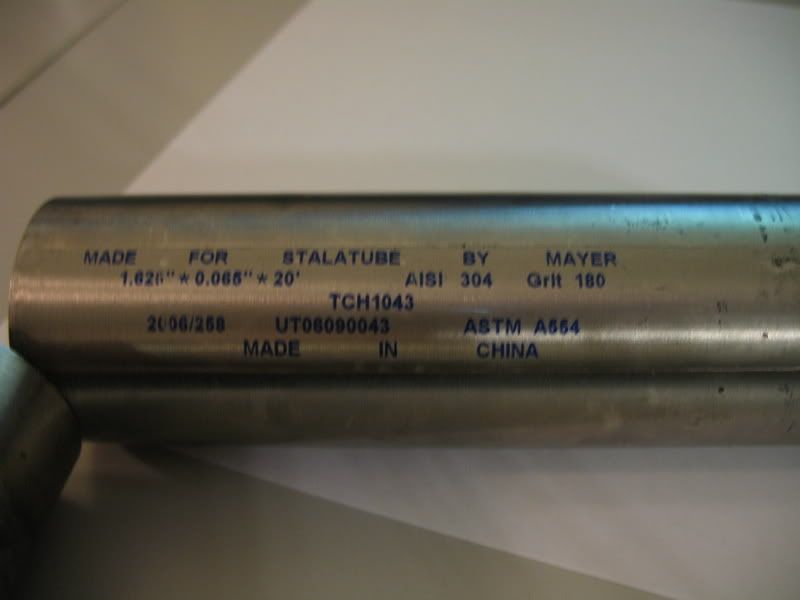
any guesses why it looks like it does? this is all a learning experience for me, and I really want to get good at this stuff!