Starting Problems
Moderator: Mike Everman
Starting Problems
Hi everyone!
I have designed and built a valved pulsejet engine for a final year project in university. The project has turned out really well up until now when I am trying to start it. I am just wondering if one of you guys with more practical experience can pick out something that Im missing that will help me.
The engine has been designed mainly using CE Tharratts equations laid out in "The Propulsive Duct". It has been designed to produce 72N (16lb) thrust, has a tailpipe diameter of 78mm (3") and is 1100mm (43") long and should operate at a frequency of 183Hz. Im using a petal valve with 10 petals which is made from 0.006" spring steel. It is fed with propane fuel injected into the engine through 6 radial 2.5mm holes which are located between 2 curved valve retainer plates so the fuel mixes with the incoming air as it rounds the edge of the valve retainer plate. The engine is being ignited on startup by a single spark plug which is fed by a spark using an automotive coil and a square-wave generator which allows me to vary the frequency of the spark from anywhere between 0.2Hz and 300Hz. Starting air is provided by a compressed air hose which can provide air at a maximum of 6 Bar.
My problem is that the engine seems to refuse to resonate. The fuel/air ignites no problem at a certain gas flow which tends to produce a nice bang and then I can hear a muffled roar from the engine as the fuel is being burned by a standing flame front it would seem. This seems to happen regardless of the spark frequency. If the air is shut off, the flame dies. If the gas is turned down the flame dies and if the gas is turned up, I get big yellow flames billowing from the tailpipe. The sound of the burning is very low as it can barely be heard over the hiss of the air-line. When I look into the front of the engine to see the valves, they do seem to be moving more than they would with only air blowing into the engine. It is very hard to see if the burn even has a frequency as it is so low it is hard to pick out the sound from the air-line sound. I have tried varying the length of the tailpipe but there is no difference. It almost sounds to me like the vacuum is not being developed within the engine to allow it to pulse. Would this make sense to any of you? I started off with a longer tailpipe of about 1300mm but as I said there seems to be no difference between what is happening now and what was happening then.
If anybody has any idea of what may be wrong I would be really grateful of the extra heads. I am so taken up with the details of this project now that I am afraid I may be missing a really simple thing and a few new heads could be a great thing. I know its hard to make judgements without actually hearing or seeing the thing but any suggestions at all would be helpful. Ill try to upload a video on youtube to explain better.
Many thanks in advance,
Thomas
I have designed and built a valved pulsejet engine for a final year project in university. The project has turned out really well up until now when I am trying to start it. I am just wondering if one of you guys with more practical experience can pick out something that Im missing that will help me.
The engine has been designed mainly using CE Tharratts equations laid out in "The Propulsive Duct". It has been designed to produce 72N (16lb) thrust, has a tailpipe diameter of 78mm (3") and is 1100mm (43") long and should operate at a frequency of 183Hz. Im using a petal valve with 10 petals which is made from 0.006" spring steel. It is fed with propane fuel injected into the engine through 6 radial 2.5mm holes which are located between 2 curved valve retainer plates so the fuel mixes with the incoming air as it rounds the edge of the valve retainer plate. The engine is being ignited on startup by a single spark plug which is fed by a spark using an automotive coil and a square-wave generator which allows me to vary the frequency of the spark from anywhere between 0.2Hz and 300Hz. Starting air is provided by a compressed air hose which can provide air at a maximum of 6 Bar.
My problem is that the engine seems to refuse to resonate. The fuel/air ignites no problem at a certain gas flow which tends to produce a nice bang and then I can hear a muffled roar from the engine as the fuel is being burned by a standing flame front it would seem. This seems to happen regardless of the spark frequency. If the air is shut off, the flame dies. If the gas is turned down the flame dies and if the gas is turned up, I get big yellow flames billowing from the tailpipe. The sound of the burning is very low as it can barely be heard over the hiss of the air-line. When I look into the front of the engine to see the valves, they do seem to be moving more than they would with only air blowing into the engine. It is very hard to see if the burn even has a frequency as it is so low it is hard to pick out the sound from the air-line sound. I have tried varying the length of the tailpipe but there is no difference. It almost sounds to me like the vacuum is not being developed within the engine to allow it to pulse. Would this make sense to any of you? I started off with a longer tailpipe of about 1300mm but as I said there seems to be no difference between what is happening now and what was happening then.
If anybody has any idea of what may be wrong I would be really grateful of the extra heads. I am so taken up with the details of this project now that I am afraid I may be missing a really simple thing and a few new heads could be a great thing. I know its hard to make judgements without actually hearing or seeing the thing but any suggestions at all would be helpful. Ill try to upload a video on youtube to explain better.
Many thanks in advance,
Thomas
-
- Posts: 3716
- Joined: Tue Dec 07, 2004 6:51 pm
- Antipspambot question: 0
- Location: 41d 1' N 80d 22' W
Re: Starting Problems
Hi motthomas,
I re-derived a lot of Tharratt's work and found his publication has lots of errors and typos in it.
IOW if you haven't rederived them, don't use them as published.
Before spending more time on getting your engine to run, let's back check your calculations.
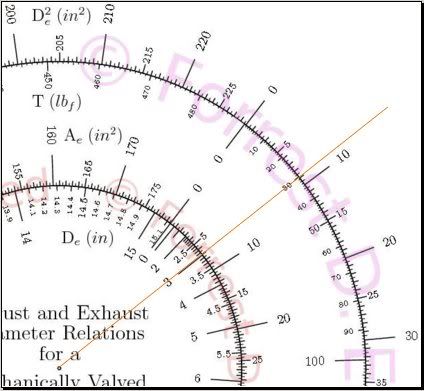
What volume is your pj? To ease the chore, you can use my calculator,
found on my thread, Computing volume … estimating cycle freq.
There is a definite relationship here.
I re-derived a lot of Tharratt's work and found his publication has lots of errors and typos in it.
IOW if you haven't rederived them, don't use them as published.
Before spending more time on getting your engine to run, let's back check your calculations.
We disagree here already. I estimate 30 lbf thrust at 3" tail pipe diameter.The engine has been designed mainly using CE Tharratts equations laid out in "The Propulsive Duct". It has been designed to produce 72N (16lb) thrust, has a tailpipe diameter of 78mm (3") and ...
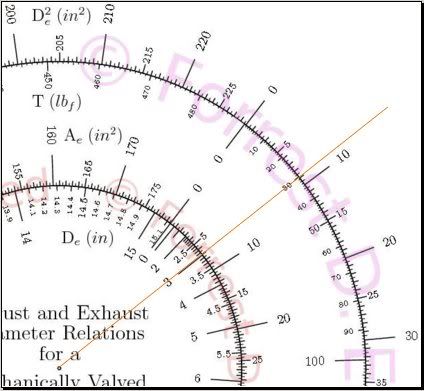
What volume is your pj? To ease the chore, you can use my calculator,
found on my thread, Computing volume … estimating cycle freq.
There is a definite relationship here.
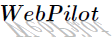
Re: Starting Problems
Thanks for the replies guys,
Webpilot: Thats surprising about Tharratts equations but it could be good if it helps me find the problem! I tried to derive them myself at the start of the project but it was unclear to me where to begin with the theory so I left it and went with the published equations. 30lbf does seem slightly more realistic though when I think about the size of the engine.
The volume of my engine is 0.20447 cubic ft. What equation can I use that in now? I presume from what you said above that Tharratts V/L=0.00316F doesnt apply? (excuse me if the equation isnt correct, I dont have my notes with me at them moment)
Ive attached a pdf of my petal valve design. Note that all dimensions are in mm unless otherwise stated. I did model the petals as simple cantilever beams and found a natural frequency of vibration of them from that. The natural frequency of the valves worked out to be 36Hz. This is another area which confuses me... I have read in a few reports about matching the frequency of operation of the engine with the natural frequency of vibration of the valves but, my understanding of the situation is that the valves are critically damped so they are not allowed to vibrate naturally. This case reduces the gain of the system to 1 and makes the valves operate at the same frequency as the engine, regardless of natural frequency of the valves. Can anybody clear this bit up for me? Am I wrong in my analysis?
What is it that determines that a certain frequency of operation of the engine is the right one? I have looked into correlating fuel burn rates with frequency but so far I have found nothing conclusive. Also, does a "megaphone" at the end of the tailpipe make an appreciable difference in performance/running characteristics?
Thanks,
Thomas
Webpilot: Thats surprising about Tharratts equations but it could be good if it helps me find the problem! I tried to derive them myself at the start of the project but it was unclear to me where to begin with the theory so I left it and went with the published equations. 30lbf does seem slightly more realistic though when I think about the size of the engine.
The volume of my engine is 0.20447 cubic ft. What equation can I use that in now? I presume from what you said above that Tharratts V/L=0.00316F doesnt apply? (excuse me if the equation isnt correct, I dont have my notes with me at them moment)
Ive attached a pdf of my petal valve design. Note that all dimensions are in mm unless otherwise stated. I did model the petals as simple cantilever beams and found a natural frequency of vibration of them from that. The natural frequency of the valves worked out to be 36Hz. This is another area which confuses me... I have read in a few reports about matching the frequency of operation of the engine with the natural frequency of vibration of the valves but, my understanding of the situation is that the valves are critically damped so they are not allowed to vibrate naturally. This case reduces the gain of the system to 1 and makes the valves operate at the same frequency as the engine, regardless of natural frequency of the valves. Can anybody clear this bit up for me? Am I wrong in my analysis?
What is it that determines that a certain frequency of operation of the engine is the right one? I have looked into correlating fuel burn rates with frequency but so far I have found nothing conclusive. Also, does a "megaphone" at the end of the tailpipe make an appreciable difference in performance/running characteristics?
Thanks,
Thomas
- Attachments
-
- engine_components.pdf
- (17.48 KiB) Downloaded 464 times
Re: Starting Problems
What is the diameter of each valve port/hole on your jet?
.20447 ft³ = 195.781 fl oz(US)
Recall the Dynajet holds 20-21 fluid ounces of water. Your jet is roughly 10 times more volume and yet you are using .006ths reeds, which are also going to me much broader. First I would guess the reeds would indent/fail if your ports are larger. Secondly, the reeds might not have enough "snap-back" with this larger engine, that is on the inflow phase, they aren't going to have much resistance and might swing open for a longer period of time than the engine likes. I had an engine that would backfire nicely, but would never catch, and when I limited the play of the reed, it sprang to life.
If you are using .006ths, maybe you could use a double or triple layer of them, I don't know. It just seems like they will need more spring and less give. And again, .006ths is likely to waffle over the hole if it can't support the pressure.
.20447 ft³ = 195.781 fl oz(US)
Recall the Dynajet holds 20-21 fluid ounces of water. Your jet is roughly 10 times more volume and yet you are using .006ths reeds, which are also going to me much broader. First I would guess the reeds would indent/fail if your ports are larger. Secondly, the reeds might not have enough "snap-back" with this larger engine, that is on the inflow phase, they aren't going to have much resistance and might swing open for a longer period of time than the engine likes. I had an engine that would backfire nicely, but would never catch, and when I limited the play of the reed, it sprang to life.
If you are using .006ths, maybe you could use a double or triple layer of them, I don't know. It just seems like they will need more spring and less give. And again, .006ths is likely to waffle over the hole if it can't support the pressure.
Last edited by Mark on Mon Feb 22, 2010 1:33 pm, edited 1 time in total.
Presentation is Everything
-
- Posts: 3716
- Joined: Tue Dec 07, 2004 6:51 pm
- Antipspambot question: 0
- Location: 41d 1' N 80d 22' W
Re: Starting Problems
Thomas,
We're still working the "kinks" out for a petal-valved pj, but the work will be valuable for future pulse-jet design work. At least, Joe and I think so. If you would like to help out, let me know.
Try calculating the thrust for a P-90. Tharrat's equation is way off here. If you used my calculator found on my thread, Computing volume … estimating cycle freq, what was its frequency estimate?The volume of my engine is 0.20447 cubic ft. What equation can I use that in now? I presume from what you said above that Tharratts V/L=0.00316F doesnt apply? (excuse me if the equation isnt correct, I dont have my notes with me at them moment)
Tharrat wrote that a petal valve can be modeled as a cantilever strip. Wrong. That's why I posted threads,Ive attached a pdf of my petal valve design. Note that all dimensions are in mm unless otherwise stated. I did model the petals as simple cantilever beams and found a natural frequency of vibration of them from that. The natural frequency of the valves worked out to be 36Hz.
- Mode 1/0
- the hunt for an easier way …
We're still working the "kinks" out for a petal-valved pj, but the work will be valuable for future pulse-jet design work. At least, Joe and I think so. If you would like to help out, let me know.
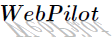
-
- Posts: 3716
- Joined: Tue Dec 07, 2004 6:51 pm
- Antipspambot question: 0
- Location: 41d 1' N 80d 22' W
Re: Starting Problems
Thomas,
I remember reading in Tharrat about where he talks about gain, etc. of a petal valve. His writing there was not unlike what's been published in numerous texts on linear one dimensional vibration theory. However, we are dealing with a non-linear phenomena and that's why I started out to verify what he was saying in my work entitled,
dynamic modeling of a strip valve (it's a sticky)
What I found there was quite unlike what Tharatt had written in his reports. I suggest you read my work.
Thanks to GRIM, he took my findings and successfully designed and built his engine. He posted his work entitled
External valve grid ] (it's a sticky)
Thomas,
The very first paper I read that dealt with, among other things, megaphone exhaust outlets, is
Gas-Dynamic Investigations of the Pulse-Jet Tube
Author(s): Shultz-Grunow, F.
Abstract: Based upon a simplified representation of the mode of operation of the pulse-jet tube, the effect of the influences mentioned in the title were investigated and it will be shown that, for a jet tube with ...
NASA Center: NACA (Unspecified Center)
Publication Year: 1947
Added to NTRS: 2005-10-13
Document ID: 20030067369; Report Number: NACA-TM-1131
This document can be found here. Even if you cannot do the graphical math, you can glean a lot from the results summaries.
I used the same mathematical technique in my thread, Dimensionless Space and Time.
This is another area which confuses me... I have read in a few reports about matching the frequency of operation of the engine with the natural frequency of vibration of the valves but, my understanding of the situation is that the valves are critically damped so they are not allowed to vibrate naturally. This case reduces the gain of the system to 1 and makes the valves operate at the same frequency as the engine, regardless of natural frequency of the valves. Can anybody clear this bit up for me? Am I wrong in my analysis?
I remember reading in Tharrat about where he talks about gain, etc. of a petal valve. His writing there was not unlike what's been published in numerous texts on linear one dimensional vibration theory. However, we are dealing with a non-linear phenomena and that's why I started out to verify what he was saying in my work entitled,
dynamic modeling of a strip valve (it's a sticky)
What I found there was quite unlike what Tharatt had written in his reports. I suggest you read my work.
Thanks to GRIM, he took my findings and successfully designed and built his engine. He posted his work entitled
External valve grid ] (it's a sticky)
Thomas,
Again, if you used my calculator, what was its frequency estimate?What is it that determines that a certain frequency of operation of the engine is the right one? I have looked into correlating fuel burn rates with frequency but so far I have found nothing conclusive. Also, does a "megaphone" at the end of the tailpipe make an appreciable difference in performance/running characteristics?
The very first paper I read that dealt with, among other things, megaphone exhaust outlets, is
Gas-Dynamic Investigations of the Pulse-Jet Tube
Author(s): Shultz-Grunow, F.
Abstract: Based upon a simplified representation of the mode of operation of the pulse-jet tube, the effect of the influences mentioned in the title were investigated and it will be shown that, for a jet tube with ...
NASA Center: NACA (Unspecified Center)
Publication Year: 1947
Added to NTRS: 2005-10-13
Document ID: 20030067369; Report Number: NACA-TM-1131
This document can be found here. Even if you cannot do the graphical math, you can glean a lot from the results summaries.
I used the same mathematical technique in my thread, Dimensionless Space and Time.
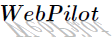
Re: Starting Problems
Yes, it does, however an engine with a magaphone exhaust has a different acoustic pattern that does not play nice with valves.Also, does a "megaphone" at the end of the tailpipe make an appreciable difference in performance/running characteristics?
Quantify the world.
-
- Posts: 3716
- Joined: Tue Dec 07, 2004 6:51 pm
- Antipspambot question: 0
- Location: 41d 1' N 80d 22' W
Re: Starting Problems
Title: Gas-Dynamic Investigations of the Pulse-Jet Tube
Title Information: Gasdynamische Untersuchungen am Verpuffungstrshlrohr; German; Parts 1 and 2
Author(s): Shultz-Grunow, F.
Abstract: Based upon a simplified representation of the mode of operation of the pulse-jet tube, the effect of the influences mentioned in the title were investigated and it will be shown that, for a jet tube with a form designed to be aerodynamically favorable, the ability to operate is at least questionable.
By taking into account the course of the development of pressure by combustion, a new insight has been obtained into the processes of motion within the jet tube, an insight that explains a number of empirical observations, namely: certain particulars of the sequence of pressure variations; the existence of an optimum valve-opening ratio; the occurrence of an intrusion of air; and the existence of a flight speed above which the jet tube ceases to operate.
At too great an opening ratio or at too great a flight speed, the continuous flow through the tube is too predominant over the oscillatory process to permit the occurrence of an explosion powerful enough to maintain continuous operation. Certain possible means of making the operation of the jet tube more independent of the flight speed and of reducing the flow losses were proposed and discussed.
Title Information: Gasdynamische Untersuchungen am Verpuffungstrshlrohr; German; Parts 1 and 2
Author(s): Shultz-Grunow, F.
Abstract: Based upon a simplified representation of the mode of operation of the pulse-jet tube, the effect of the influences mentioned in the title were investigated and it will be shown that, for a jet tube with a form designed to be aerodynamically favorable, the ability to operate is at least questionable.
By taking into account the course of the development of pressure by combustion, a new insight has been obtained into the processes of motion within the jet tube, an insight that explains a number of empirical observations, namely: certain particulars of the sequence of pressure variations; the existence of an optimum valve-opening ratio; the occurrence of an intrusion of air; and the existence of a flight speed above which the jet tube ceases to operate.
At too great an opening ratio or at too great a flight speed, the continuous flow through the tube is too predominant over the oscillatory process to permit the occurrence of an explosion powerful enough to maintain continuous operation. Certain possible means of making the operation of the jet tube more independent of the flight speed and of reducing the flow losses were proposed and discussed.
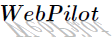
Re: Starting Problems
Again, thank you very much for all the input webpilot! Ive downloaded the paper by Shultz-Grunow and I will read it tonight.
When I say I modelled the valve as a cantilever I mean I modelled it as a cantilever beam with a lumped mass along its length to make up for the extra inertial mass of the petal. Very much the same way as you did in your thread "the hunt for an easier way" except not quite as accurate because my calculations were carried out on the back of a note-pad in the middle of a lecture when the idea popped into my head.
I never went back and calculated it more accurately after I figured out the critically damped motion.
Using your .exe file to calculate the volume (very handy tool by the way!) I got an estimate for the frequency of operation of the jet as 110Hz. Thats pretty low in comparison to the 183Hz I had previously calculated but as Im beginning to figure out, Tharrats equations arent the most accurate!
Concerning the shape of the jet body: When I enter a required thrust of 30lbf into Eric Becks Pulsejet calculator file available on this site, I get very similar dimensions to those of my jet. With one noteable difference though... the reducing cone from the combustion chamber diameter down to tailpipe diameter is much longer in the calculator than it is in my jet. Is the shape of this reduction essential to the running of the engine?
@ Mark, I never really thought about the valve material being too light. I started my research in the project by reading a previous final year report from my university which was conducted by another student 6 years ago. He built a similar sized engine as mine and had used 0.008" steel for the valves. His engine pulsed but could not run without the external supply of air. He ran out of time to do further testing but he concluded that he thought he had used too heavy a valve material which was not opening enough to allow the suffiecient volume of air to enter the engine during the intake phase. To try and avoid this same problem I chose to use the lighter 0.006" material from the start. Maybe his problem was the same you have described? I have a second petal valve in decent condition so I will try a quick test first thing in the morning and see if that makes any difference! Did your engine exhibit the same muffled burning after the backfires?
And I have attached my designs of valve plate in pdf form. The first drawing is the valve plate designed using the 0.2Ae rule and assuming a 50% valve efficiency. (this was taken from Tharratts paper though so Im not sure abiout the accuracy of this equation?) The second valve plate is one which I had machined at the same time as a sort of backup in case the valve area was not big enough in the first one. I have never tested the engine with this valve plate in place.
When I say I modelled the valve as a cantilever I mean I modelled it as a cantilever beam with a lumped mass along its length to make up for the extra inertial mass of the petal. Very much the same way as you did in your thread "the hunt for an easier way" except not quite as accurate because my calculations were carried out on the back of a note-pad in the middle of a lecture when the idea popped into my head.

Using your .exe file to calculate the volume (very handy tool by the way!) I got an estimate for the frequency of operation of the jet as 110Hz. Thats pretty low in comparison to the 183Hz I had previously calculated but as Im beginning to figure out, Tharrats equations arent the most accurate!
Concerning the shape of the jet body: When I enter a required thrust of 30lbf into Eric Becks Pulsejet calculator file available on this site, I get very similar dimensions to those of my jet. With one noteable difference though... the reducing cone from the combustion chamber diameter down to tailpipe diameter is much longer in the calculator than it is in my jet. Is the shape of this reduction essential to the running of the engine?
@ Mark, I never really thought about the valve material being too light. I started my research in the project by reading a previous final year report from my university which was conducted by another student 6 years ago. He built a similar sized engine as mine and had used 0.008" steel for the valves. His engine pulsed but could not run without the external supply of air. He ran out of time to do further testing but he concluded that he thought he had used too heavy a valve material which was not opening enough to allow the suffiecient volume of air to enter the engine during the intake phase. To try and avoid this same problem I chose to use the lighter 0.006" material from the start. Maybe his problem was the same you have described? I have a second petal valve in decent condition so I will try a quick test first thing in the morning and see if that makes any difference! Did your engine exhibit the same muffled burning after the backfires?
And I have attached my designs of valve plate in pdf form. The first drawing is the valve plate designed using the 0.2Ae rule and assuming a 50% valve efficiency. (this was taken from Tharratts paper though so Im not sure abiout the accuracy of this equation?) The second valve plate is one which I had machined at the same time as a sort of backup in case the valve area was not big enough in the first one. I have never tested the engine with this valve plate in place.
- Attachments
-
- Valve plates.pdf
- (33.87 KiB) Downloaded 455 times
Re: Starting Problems
Hi Thomas,
Just edited my post, noticed in the previous post your engine is not a straight piper.
What are the as built dimensions? length of CC, length of reducing cone, length of tailpipe, dia. of CC? Intake length?
Size of fuel lines? Size of propane tank?
The biggest sin I spot (for now) is injecting the propane within the CC. Am sure by now you have seen propane is somewhat a thick gas and is troublesome to acquire a good air fuel ratio, going rich or lean. If it were me, I would move the injection point where most engines have them, in the venturi (illustrated by blue dot). IMO the propane traveling through the valve holes and past the valves themselves will aid in mixing, also the longer path will allow more time for distribution.
One thing GRIM mentioned in the past is that intake length is important to achieve a running engine.
The propane injection holes look a little biggish in diameter. This may be creating havoc, with a rich condition. May want to try 6 holes near 1.0mm.
Hope this helps, Joe
Also do you have a regulator on the propane tank? (Gees, why didn't I ask that question first.
)
Just edited my post, noticed in the previous post your engine is not a straight piper.
What are the as built dimensions? length of CC, length of reducing cone, length of tailpipe, dia. of CC? Intake length?
Size of fuel lines? Size of propane tank?
The biggest sin I spot (for now) is injecting the propane within the CC. Am sure by now you have seen propane is somewhat a thick gas and is troublesome to acquire a good air fuel ratio, going rich or lean. If it were me, I would move the injection point where most engines have them, in the venturi (illustrated by blue dot). IMO the propane traveling through the valve holes and past the valves themselves will aid in mixing, also the longer path will allow more time for distribution.
One thing GRIM mentioned in the past is that intake length is important to achieve a running engine.
The propane injection holes look a little biggish in diameter. This may be creating havoc, with a rich condition. May want to try 6 holes near 1.0mm.
Hope this helps, Joe
Also do you have a regulator on the propane tank? (Gees, why didn't I ask that question first.

- Attachments
-
- straight.JPG (9.4 KiB) Viewed 11696 times
Last edited by PyroJoe on Mon Feb 22, 2010 7:03 pm, edited 8 times in total.
Re: Starting Problems
After your valve post I see your valve plate is 157mm or about 6 inches in diameter, yet your petal valves aren't taking advantage of using the extra space. In this case your petal valves may be OK for a few runs. If you had put them out nearer the edge of the valve plate, you could have had more valve area, either by making the holes a bit bigger or just making more of them. Perhaps your jet is a little on the low side for valve area, but I'm just shooting from the hip. A bigger jet like that will sometimes need a lot of starting air. I should think .008ths reeds would be a better choice, but again since your ports are in closer to the center of the plate, that makes the ten holes a bit smaller. Still I can't tell just how wide they are - an actual picture of your engine would go a long way to understanding what's what. Also, I'm not sure how much of your valve plate might be flange inside/outside of the combustion chamber.@ Mark, I never really thought about the valve material being too light. I started my research in the project by reading a previous final year report from my university which was conducted by another student 6 years ago. He built a similar sized engine as mine and had used 0.008" steel for the valves. His engine pulsed but could not run without the external supply of air. He ran out of time to do further testing but he concluded that he thought he had used too heavy a valve material which was not opening enough to allow the suffiecient volume of air to enter the engine during the intake phase. To try and avoid this same problem I chose to use the lighter 0.006" material from the start. Maybe his problem was the same you have described? I have a second petal valve in decent condition so I will try a quick test first thing in the morning and see if that makes any difference! Did your engine exhibit the same muffled burning after the backfires?
Might the jet have been a little starved for valve area and he interpreted that as having too thick of petals?"He built a similar sized engine as mine and had used 0.008" steel for the valves. His engine pulsed but could not run without the external supply of air. He ran out of time to do further testing but he concluded that he thought he had used too heavy a valve material which was not opening enough to allow the suffiecient volume of air to enter the engine during the intake phase. To try and avoid this same problem I chose to use the lighter 0.006" material from the start."
I imagine you will have plenty of noise when you get it running.
Best of luck,
Mark
Presentation is Everything
Re: Starting Problems
The first valve head with the smaller holes appears to have approx. 46.3% intake to exhast ratio.
The one with the larger holes appears to be approx. 78%
The larger holed version has my vote, with the provision that the valve material has a viable thickness.
This engine could require a significant amount of propane, smaller tanks will tend to "chill" quickly, degrading the available fuel flow.
Joe
The one with the larger holes appears to be approx. 78%
The larger holed version has my vote, with the provision that the valve material has a viable thickness.
This engine could require a significant amount of propane, smaller tanks will tend to "chill" quickly, degrading the available fuel flow.
Joe
-
- Posts: 3716
- Joined: Tue Dec 07, 2004 6:51 pm
- Antipspambot question: 0
- Location: 41d 1' N 80d 22' W
Re: Starting Problems
If you don't get the driving frequency ratio correct, the valves may simply operate out of phase with the driving pressure
- open during combustion
- closed during intake
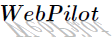
Re: Starting Problems
Yeah,
180 out of phase would be a bad deal.
180 out of phase would be a bad deal.