Several questions about design
Moderator: Mike Everman
Several questions about design
Hello, I'm relatively new to the world of pulse jet building. I've gone over a lot of stuff and read through a couple of books and it seems the more I try to find answers the more questions I have. As mentioned a lot, in general not a lot of new research has been done on standard pulse-jet design. So here are some questions that hopefully you all have some answers or thoughts about.
In Bruce's book "The Enthusiast's Guide to Pulse Jets" he mentions a few things I couldn't find reference to anywhere else.
Has anyone else built the dual-disc cover between the valves and the combustion chamber? Does it really increase efficiency and increase valve-life?
Also, does releasing fuel from between those plates do as good a job at atomizing as he claims?
Does cooling the tailpipe increase efficiency/thrust? Would ribbing help this? Has anyone ever hooked up a sterling engine to the tailpipe? Also, would putting the pulsejet in a duct do the same thing by forcing the cold air around it?
Does the tailpipe have to be straight or can it be curved for space concerns? I saw that a lockwood design could do this, but was unsure of a standard valved one.
What is the best type of valve configuration for efficiency?
Is there any sort of calculator that takes into account an augmentor? As in, I could build a 40lb thrust valved pj, or a 30lb thrust pj with augmentor of this shape and get 40lbs.
And last, has anyone ever increased the surface area of the combustion chamber by adding dimples, ridges, etc in order to make the gas more active and combust more thoroughly? I know this has been done with success on an ICE and the random grooves cause the gases to disperse more thoroughly and ignite better.
I'm sorry for the long post. It's just very hard to find specific information on pulse jets. It seems like you just have to experiment a lot to find out anything because there's no research to support things either way. Well, I appreciate any help. Thanks.
In Bruce's book "The Enthusiast's Guide to Pulse Jets" he mentions a few things I couldn't find reference to anywhere else.
Has anyone else built the dual-disc cover between the valves and the combustion chamber? Does it really increase efficiency and increase valve-life?
Also, does releasing fuel from between those plates do as good a job at atomizing as he claims?
Does cooling the tailpipe increase efficiency/thrust? Would ribbing help this? Has anyone ever hooked up a sterling engine to the tailpipe? Also, would putting the pulsejet in a duct do the same thing by forcing the cold air around it?
Does the tailpipe have to be straight or can it be curved for space concerns? I saw that a lockwood design could do this, but was unsure of a standard valved one.
What is the best type of valve configuration for efficiency?
Is there any sort of calculator that takes into account an augmentor? As in, I could build a 40lb thrust valved pj, or a 30lb thrust pj with augmentor of this shape and get 40lbs.
And last, has anyone ever increased the surface area of the combustion chamber by adding dimples, ridges, etc in order to make the gas more active and combust more thoroughly? I know this has been done with success on an ICE and the random grooves cause the gases to disperse more thoroughly and ignite better.
I'm sorry for the long post. It's just very hard to find specific information on pulse jets. It seems like you just have to experiment a lot to find out anything because there's no research to support things either way. Well, I appreciate any help. Thanks.
-
- Posts: 887
- Joined: Wed Dec 24, 2003 12:12 pm
- Antipspambot question: 0
- Location: France
- Contact:
Re: Several questions about design
I don't know if anyone here has done it. It would be relatively simple to test if you build a head that can do both. It's a bit "suck it and see", I think.timwylie wrote:Hello, I'm relatively new to the world of pulse jet building. I've gone over a lot of stuff and read through a couple of books and it seems the more I try to find answers the more questions I have. As mentioned a lot, in general not a lot of new research has been done on standard pulse-jet design. So here are some questions that hopefully you all have some answers or thoughts about.
In Bruce's book "The Enthusiast's Guide to Pulse Jets" he mentions a few things I couldn't find reference to anywhere else.
Has anyone else built the dual-disc cover between the valves and the combustion chamber? Does it really increase efficiency and increase valve-life?
Also, does releasing fuel from between those plates do as good a job at atomizing as he claims?
I would personally doubt if it makes an appreciable difference to thrust, either way.Does cooling the tailpipe increase efficiency/thrust? Would ribbing help this?
A stirling engine is a good idea for utilising some of the waste heat, especially from the combustion chamber. Like I said, a doubt if it would make much difference to the efficiency or thrust of the jet itself, but you'd be extracting otherwise "lost" energy and increasing the efficiency of the overall system. Unless producing radiant heat and noise is your goal :)Has anyone ever hooked up a sterling engine to the tailpipe? Also, would putting the pulsejet in a duct do the same thing by forcing the cold air around it?
Ducting a jet is a reasonable idea, as long as your duct doesn't affect the acoustics of the engine. It makes mounting much easier by keeping the radiant heat away from nearby structures, and if well-designed can decrease the speed, and increase the density of, the airflow around the jet; this allows for a heavier "charge" to be pulled back into the tailpipe, and may well increase thrust (a significant amount of the massflow, and thus thrust, is from the "cold" air "plug" pulled back into the tailpipe).
A curved tailpipe is not a problem, although curves make the acoustics difficult to work out. Best way to deal with this is with a slightly shorter than "design" tailpipe, and a sliding sleeve at the end that can be adjusted when testing.Does the tailpipe have to be straight or can it be curved for space concerns? I saw that a lockwood design could do this, but was unsure of a standard valved one.
No valves at all. Helps to increase valve life, too.What is the best type of valve configuration for efficiency?
The improved, postwar Argus jet achieved a fuel efficiency (TSFC) of 3.0Kg thrust/Kg fuel/Hour according to Messerschmidt's tests in the 50s. The same tests gave the stock SNECMA "Escopette" 1.8. The "Chinese" design produces results in a similar range. The Kentfield design has been tweaked to at least equal the Escopette, and get better than twice the efficiency of the Argus. Hiller claimed a 1.0 TSFC, but I haven't found anything apart from Hiller's claims to back that up - Lockwood's paper indicated a best TSFC of 1.66.
Not to my knowledge, although I'm sure someone will pile in and say "yes there is". About the "best" augmentor I've seen thus far is Eric's (see below), although it's not terribly fuel-efficient.Is there any sort of calculator that takes into account an augmentor? As in, I could build a 40lb thrust valved pj, or a 30lb thrust pj with augmentor of this shape and get 40lbs.
http://www.youtube.com/watch?v=b0KJwa5iWTY
A "normal" augmentor will likely improve efficiency more than any other improvement you can make. Lockwood's US Navy report indicated TSFC dropping from 1.66 to 1.16 just by adding an augmentor. Lockwood's results also indicated that the augmentor provided as much thust as, and usually more than, the jet itself.
SNECMA / Messerschmidt's dual mode pulse / ram jet had an interior "sleeve" to the combustion chamber, this was intended to keep some burning gases around at high speed operation (a radial flameholder, if you will). I don't remember if they did tests with and without in pulsejet operation, though. You can see it here:And last, has anyone ever increased the surface area of the combustion chamber by adding dimples, ridges, etc in order to make the gas more active and combust more thoroughly? I know this has been done with success on an ICE and the random grooves cause the gases to disperse more thoroughly and ignite better.
There's a fair amount of research out there, but a lot of it is "hidden" or difficult to find. The search facility here helps to unearth most of what's available, though.I'm sorry for the long post. It's just very hard to find specific information on pulse jets. It seems like you just have to experiment a lot to find out anything because there's no research to support things either way. Well, I appreciate any help. Thanks.
Re: Several questions about design
Thanks for the reply. That cleared up quite a bit, and gives me some direction for more research. I have been searching the forums, but it's hard to find very specific things.
I know the design of a valveless is very attractive, but for a specific size, isn't a valved pulse jet more powerful? I also need a design where the intake is in front.
I know the design of a valveless is very attractive, but for a specific size, isn't a valved pulse jet more powerful? I also need a design where the intake is in front.
-
- Posts: 144
- Joined: Sat Sep 26, 2009 9:59 pm
- Antipspambot question: 125
Re: Several questions about design
If you read about Liquid Fuel Rocket engines you will learn, heat is expanding gas, expandng gas = thrust. So technical if you cool a pulse jet with water it should reduce the thrust. If you cover the entire engine with a shroud and use the exhaust to make air flow over the whole engine like an augmentor technical it should produce more thrust with all the hot engine heat flowing out the end with the exhaust. I have not tried it yet but who knows, it may work great.
Dual-disc covers between the valves and the combustion chamber does not protect the reed valves. It is the design of the disc cover and the design of the engine that protects the reed valves. Once the engine is hot the 2 discs become hot and if your using liquid fuel spraying out between 2 hot discs it helps to vaporize the fuel.
I have experemented with several types of reed valves and efficency is about the same if they are all designed correctly. The valves have to close tight enough for the engine to suck enough vacuum to maintain combustion in the combustion chamber. If the vacuum is too low the engine will not run. Several people claim Argus valves are more efficient but that is not exactly 100% true. Air flows straight through Argus valve so that makes them seem like they should be more efficent. Argus valves need to be shorter than petal valves or use stronger spring steel so air flowing threw them has enough vacuum during the low pressure cycle of the engine to keep the engine running. If you can lower the pressure inside the engine even more during the low pressure cycle it force the engine to breath in a larger fuel/air mixture producing more thrust. What some people would call less efficient valves can actually make the engine have more thrust. What I would call low efficient valves are valves that completely restrict air flow.
Another thing you will learn reading about Liquid Fuel Rocket Engines is each fuel as its own burn rate. A pulse jet engine combustion chamber needs to be made larger for slow burning fuels and made smaller for fast buring fuels. Fast burning fuels produce a much harder explosion in the combustion chamber than slow buring fuels. Fast buring fuels tend to hammer the reed valves shut very hard causing damage while slow buring fuels tend to be more of a push than a hammer.
Every time you make a change to a pulse jet engine it effects the design of the whole engine and you have to change something else to compensate for it.
Dual-disc covers between the valves and the combustion chamber does not protect the reed valves. It is the design of the disc cover and the design of the engine that protects the reed valves. Once the engine is hot the 2 discs become hot and if your using liquid fuel spraying out between 2 hot discs it helps to vaporize the fuel.
I have experemented with several types of reed valves and efficency is about the same if they are all designed correctly. The valves have to close tight enough for the engine to suck enough vacuum to maintain combustion in the combustion chamber. If the vacuum is too low the engine will not run. Several people claim Argus valves are more efficient but that is not exactly 100% true. Air flows straight through Argus valve so that makes them seem like they should be more efficent. Argus valves need to be shorter than petal valves or use stronger spring steel so air flowing threw them has enough vacuum during the low pressure cycle of the engine to keep the engine running. If you can lower the pressure inside the engine even more during the low pressure cycle it force the engine to breath in a larger fuel/air mixture producing more thrust. What some people would call less efficient valves can actually make the engine have more thrust. What I would call low efficient valves are valves that completely restrict air flow.
Another thing you will learn reading about Liquid Fuel Rocket Engines is each fuel as its own burn rate. A pulse jet engine combustion chamber needs to be made larger for slow burning fuels and made smaller for fast buring fuels. Fast burning fuels produce a much harder explosion in the combustion chamber than slow buring fuels. Fast buring fuels tend to hammer the reed valves shut very hard causing damage while slow buring fuels tend to be more of a push than a hammer.
Every time you make a change to a pulse jet engine it effects the design of the whole engine and you have to change something else to compensate for it.
-
- Posts: 3716
- Joined: Tue Dec 07, 2004 6:51 pm
- Antipspambot question: 0
- Location: 41d 1' N 80d 22' W
Re: Several questions about design
I disagree.
If you cool the gases in the exhaust pipe, you increase the gas's density. If you increase the density of the expelled gases and if their exhaust speed remains the same or increases, then you've increased their momentum component in the axial direction, m·v per cycle.
From the conservation of momentum, the greater the momentum expelled, the greater the momentum transferred to the engine, or the greater the airframe's speed in the opposite direction.
The analogy is like throwing heavier snowballs when you're on ice skates.
Then you come to another term that is used not quite correctly when it comes to pulse-jets and that is thrust. You can compute an average thrust over one cycle, but the correct term to use is impulse or F·Δt which is directly associated with the time rate of change of momentum.
Mathematically speaking (bold quantities denote vectors),
F = dp/dt = d(m·v)/dt
F·Δt = dp = d(m·v)
where:
If you cool the gases in the exhaust pipe, you increase the gas's density. If you increase the density of the expelled gases and if their exhaust speed remains the same or increases, then you've increased their momentum component in the axial direction, m·v per cycle.
From the conservation of momentum, the greater the momentum expelled, the greater the momentum transferred to the engine, or the greater the airframe's speed in the opposite direction.
The analogy is like throwing heavier snowballs when you're on ice skates.
Then you come to another term that is used not quite correctly when it comes to pulse-jets and that is thrust. You can compute an average thrust over one cycle, but the correct term to use is impulse or F·Δt which is directly associated with the time rate of change of momentum.
Mathematically speaking (bold quantities denote vectors),
F = dp/dt = d(m·v)/dt
F·Δt = dp = d(m·v)
where:
- F is a force (a pressure times area) at some particular time;
force is a vector quantity - Δt is time increment
- F·Δt is an engineering term, defined as impulse
- p is the momentum, a vector quantity
- dp/dt is the time rate of change of momentum
- m is mass and
- v is the velocity of the gases
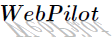
-
- Posts: 887
- Joined: Wed Dec 24, 2003 12:12 pm
- Antipspambot question: 0
- Location: France
- Contact:
Re: Several questions about design
If you read about bicycles you will learn, greater force applied to the pedals = greater thrust. So technically, it doesn't matter what you do to a pulse jet, because it has no pedals. Or tyres. Hell, it doesn't even have a chain.Rocket Man wrote:If you read about Liquid Fuel Rocket engines you will learn, heat is expanding gas, expandng gas = thrust. So technical if you cool a pulse jet with water it should reduce the thrust.
Yes, that was sarcasm. For those over the "other side of the pond" who don't understand the concept, replace the preceding paragraph with the single word "rubbish".
Rockets, pulse jets, etc, all work by inducing mass flow in a particular direction. Yes, they generally do this by using heat to cause gas expansion, but that's merely a mechanism to induce massflow, rather than an end in and of itself. Indeed, if you consider the french term for this type of motor, "moteur à réaction", we get a considerable hint as to how they work - as Forrest has explained in a somewhat technical manner above, this is by applying Newton's third law.
A closer analogy to a pulsejet in this respect is probably the modern "high bypass" jet engine - a significant amount of the thrust produced is given by the relatively cold gas mass entrained by the hot gas jet (and in the case of a pulsejet, that which is "sucked back up the tailpipe"). I'll leave it to you to decide if cooling the tailpipe (and thus increasing the mass of gas in the tailpipe) is a good idea or not.
-
- Posts: 5007
- Joined: Fri Oct 31, 2003 7:25 am
- Antipspambot question: 0
- Location: santa barbara, CA
- Contact:
Re: Several questions about design
Bwa ha hatufty wrote:No valves at all. Helps to increase valve life, too.
The Lockwood Hiller reported TSFC of 1 was with both intake and exhaust augmenters.tufty wrote:The improved, postwar Argus jet achieved a fuel efficiency (TSFC) of 3.0Kg thrust/Kg fuel/Hour according to Messerschmidt's tests in the 50s. The same tests gave the stock SNECMA "Escopette" 1.8. The "Chinese" design produces results in a similar range. The Kentfield design has been tweaked to at least equal the Escopette, and get better than twice the efficiency of the Argus. Hiller claimed a 1.0 TSFC, but I haven't found anything apart from Hiller's claims to back that up - Lockwood's paper indicated a best TSFC of 1.66.
I hope everyone has a great new year!
Mike Often wrong, never unsure.
__________________________
__________________________
-
- Posts: 887
- Joined: Wed Dec 24, 2003 12:12 pm
- Antipspambot question: 0
- Location: France
- Contact:
Re: Several questions about design
Ah, you learn something new every day. That makes sense, though.Mike Everman wrote:The Lockwood Hiller reported TSFC of 1 was with both intake and exhaust augmenters.
I probably have the papers somewhere, but any hint as to which particular document covers this?
Happy new year and all that,
simon
-
- Posts: 115
- Joined: Wed Oct 01, 2008 7:39 pm
- Antipspambot question: 125
- Location: The Netherlands
Re: Several questions about design
I've searched over the whole forum, but I never founded something about how tho make this augmentors, or what the dimensions for a augmentor for an lockwood hiller pulsejet would be.
I already have this documents, but the dimensions I get from the augmentor parameters seems very curious
viewtopic.php?f=3&t=5132
Is there maybe anyone who has more information about designing augmentors
Also happy new year
I already have this documents, but the dimensions I get from the augmentor parameters seems very curious

viewtopic.php?f=3&t=5132
Is there maybe anyone who has more information about designing augmentors
Also happy new year

...It's better to generate heat efficiently, than recover it efficiently...
-
- Posts: 421
- Joined: Mon Feb 16, 2009 9:26 pm
- Antipspambot question: 0
- Location: The Netherlands
Re: Several questions about design
Puchie,
I should have somewhere lot's of research documents about ejectors, showing the best (and worse) designs.
I was already planning to open a topic about ejectors, now hopefully sooner (I'm not that fast...
)
But where to open? In valved, valveless, tools, ...?
Fedde
I should have somewhere lot's of research documents about ejectors, showing the best (and worse) designs.
I was already planning to open a topic about ejectors, now hopefully sooner (I'm not that fast...

But where to open? In valved, valveless, tools, ...?
Fedde
Your scepticism is fuel for my brain.
Re: Several questions about design
a question on TSFC calculation
The following reserch paper stated the exit gas velocity of a dynajet-type pulse combustor varies from 40m/s to 130m/s in a cycle, and the average value is smaller than 100m/s.
http://serve.me.nus.edu.sg/arun/file/te ... ustion.pdf
http://serve.me.nus.edu.sg/arun/proj_un ... _06-07.htm
Assume the exit gas velocity=100m/s, fuel to air mix ratio=1:20, g=10m/s^2
specific impulse=20*100m/s/(10m/s^2)=200 seconds
by definition of TSFC
http://en.wikipedia.org/wiki/Thrust_spe ... onsumption
TSFC=3600/200=18, which is 10 times of the Escopette
How could real pulsejets (even the worst) consume far less fuel than theory?
entrained cold air in the tailpipe? In figure above, exit gas velocity never drop below 0.
fuel to air mix ratio 10 times smaller(extremely lean combustion)? The paper stated the excess air ratio is 1.00-1.01.
The following reserch paper stated the exit gas velocity of a dynajet-type pulse combustor varies from 40m/s to 130m/s in a cycle, and the average value is smaller than 100m/s.
http://serve.me.nus.edu.sg/arun/file/te ... ustion.pdf
http://serve.me.nus.edu.sg/arun/proj_un ... _06-07.htm
Assume the exit gas velocity=100m/s, fuel to air mix ratio=1:20, g=10m/s^2
specific impulse=20*100m/s/(10m/s^2)=200 seconds
by definition of TSFC
http://en.wikipedia.org/wiki/Thrust_spe ... onsumption
TSFC=3600/200=18, which is 10 times of the Escopette
How could real pulsejets (even the worst) consume far less fuel than theory?
entrained cold air in the tailpipe? In figure above, exit gas velocity never drop below 0.
fuel to air mix ratio 10 times smaller(extremely lean combustion)? The paper stated the excess air ratio is 1.00-1.01.